Optimizing the Balance Between People, Information Systems and Automation
May 23, 2023 By: Louis J. Cerny | Topics: Supply Chain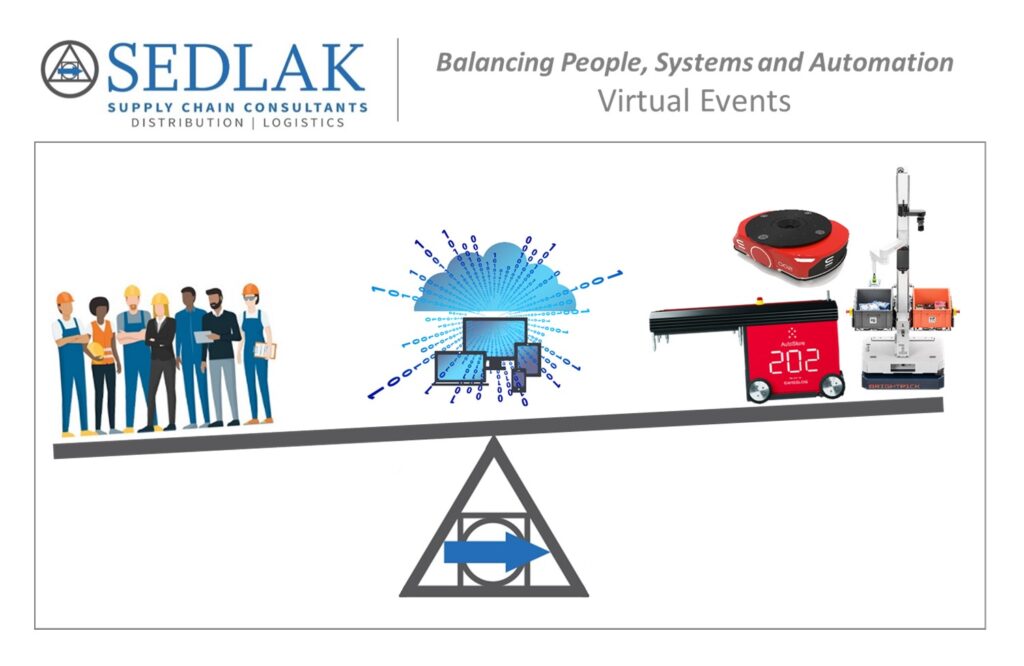
It was great to see that ProMat was so well attended this year! After the past few years it was good to reconnect with friends and colleagues.
Balance
Achieving balance is a critical part of life, whether it is walking a tightrope, balancing our careers and family life, or determining the optimal mix of people, systems and automation in fulfillment operations. Finding that balance is challenging but highly rewarding. While I can’t help you with the first two balancing challenges, there are many options to successfully address the third.
It was amazing to see all the automation options that have become available in the last year. From automated trailer unloaders from Boston Dynamics and Green Pickle to AMRs and AGVs that continue to increase functionality. The options will only continue to grow to meet the demand for faster customer service at lower costs. Companies can no longer expect to add people to meet these demands. Even with the economy showing signs of slowing, companies can still not fill positions to meet demand.
While the need for labor in fulfillment should continue to be eased by adding automation, most organizations will still require people to meet the needs of their customers. Obtaining the appropriate balance between people, systems and automation will be a challenge that all organizations will need to address.
People
All our clients, regardless of the market and services they provide, start every discussion with the fact that despite paying increasing wages, they cannot find sufficient people to meet their needs.
There are only so many options to address this challenge:
- Continue to increase compensation
- Reduce turnover
- Implement automation
Increasing compensation can only do so much since the cost associated with fulfillment labor needs to be minimized to compensate for higher transportation, and turnover will continue to be a challenge as people will leave to go down the street for an increase, often less than a dollar per hour. A way to counteract this trend is to reward those associates who are performing at a higher level while at the same time challenging the underachievers to improve their performance. To do this effectively, we recommend implementing a Labor Management System. This is a trend that is seeing as much interest as we have seen in the last 20 years. An effective system will result in cost savings by reducing missing or unproductive time and increasing performance. Retaining your workforce provides additional savings by reducing your hiring and training costs. An LMS will typically provide savings of 10%-15% and will reduce turnover.
Today’s systems can do much more than in the past. Today’s systems can provide significant reporting capabilities and financial data along with being able to develop system-generated standards, therefore minimizing the need for engineered standards and the ongoing support. If you haven’t considered LMS recently I strongly recommend looking into one.
Regardless of whether you are bringing in an LMS or automation, the common critical item of the process is the information systems that are required to communicate, control and coordinate the overall flow of the operation. It is critical to include your information systems team in any project impacting the operation. Without their understanding and support of the goals and objectives of the project, I can guarantee that you will not have a successful initiative. Including them in the RFP process will ensure that the systemic functionality and security will be addressed proactively. Today’s increasing automation will require systems that can easily interface with multiple pods of automation from multiple vendors.
Today there are multiple options for automation from receiving though shipping. Selecting the best solution for your fulfillment operation is a daunting task. While it is good to have options, when deciding on which ones to consider, I suggest that you take a step back before you jump in.
We have found the following approach to be highly effective:
- Flow chart the operation from receiving through shipping and returns
- Identify operations that have:
- High labor
- Long travel distances
- Steady versus highly seasonal volume
- Prioritize the functions to address
- Review the options for:
- Investment
- Space required
- Labor
- Flexibility
- Scalability
- Develop the business case
Another factor to consider is whether the option can be provided as a service versus capital investment. AMRs are typically provided this way, but we have heard that GTP solutions are now considering pay-as-you-go options.
Achieving balance is easier with a trusted advisor
As mentioned previously, it is good to have options, but too many options can be overwhelming. We can certainly partner with you on this journey as we have for our clients over the past 65 years.
We also invite you to attend our Virtual series on Balancing People, Systems and Automation.
The 90-minute events will be held starting in June and going through September. Each event will cover a portion of this challenge and will provide insight, case studies, lessons learned and recommendations from industry leading suppliers, their customers and our staff. We look forward to seeing you there, so click here to register for free.
Questions? Contact Sedlak Vice President Lou Cerny at lcerny@jasedlak.com for more information or to discuss your supply chain needs.